

Bleach Areation-In Process C-41, you must aerate the bleach to convert the less active iron II into more active iron III. Retained silver is caused by a bleach cycle time that is too short, a bleach temperature too low, or a bleach that is too dilute, underreplenished, or not aerated adequately. This can effect the scanning and printing of films, causing an overall increase in the contrast of the print, as well as causing highlight areas to be lacking in detail. If bleaching is inadequate, it can cause retained silver because not all of the metallic silver is converted to silver halide. Bleach aeration adds oxygen needed to convert the reduced bleaching agent into an active form. Replenishment rate, mixing procedures, and aeration efficiency affect the chemical concentrations. Time, agitation, and temperature affect the rate of diffusion. Bleach concentration and the rate at which the solution diffuses into the emulsion affect bleach activity. The silver halide is later dissolved in the fixer. Bleach In the film process, the bleach stops developer activity and converts metallic silver produced in the developer step into silver halide. With too much developer activity, too much dye forms with too little activity, not enough dye forms.
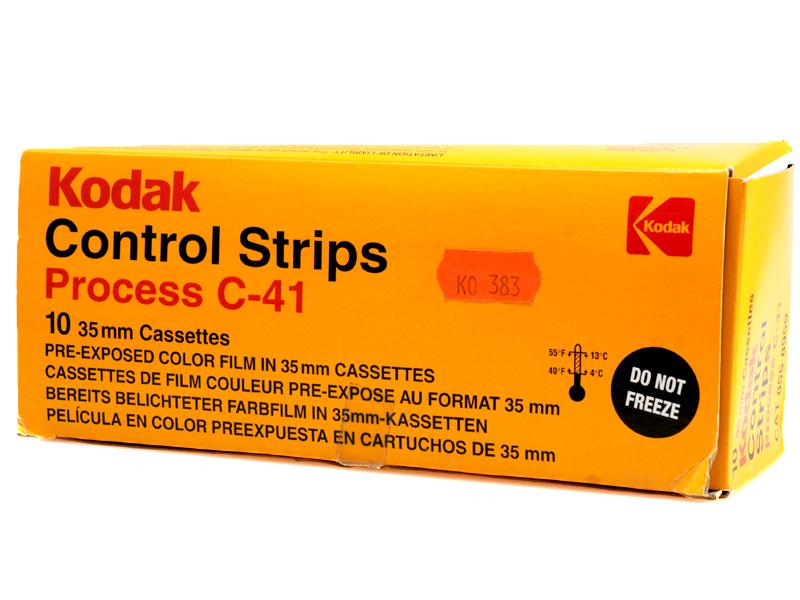
Time, temperature, and agitation affect the diffusion rate. Temperature, time, concentration, replenishment rate, agitation, and the rate at which solutions diffuse into the emulsion affect developer activity. The amount of cyan, magenta, and yellow dye formed depends on exposure and developer activity. It is later removed by bleaching and fixing. Once the dye image has formed, there is no need for the silver image.

At the same time, the color developing agent in the developer oxidizes and combines with the dye couplers at the site of the silver image in each of the dye-forming emulsion layers to form a color image. Developer The developer chemically reduces the exposed silver halide in the film or paper to form a metallic silver image. Understanding the function of each solution can help you diagnose processing problems. Tank Solution-The solution used in the processor tank often referred to as “working solution.”ĮFFECTS OF PROCESSING SOLUTIONS Each solution affects the film or paper differently. Starter-A concentrate that is added during preparation of a fresh tank solution so that it will yield results similar to those provided by a seasoned tank solution. The chemical components and seasoning by-products of a seasoned solution are at an optimum level for processing. Seasoned Solution-A tank solution that has been used and replenished for a period of time. Replenisher-Solution used to restore the chemical components of the tank solution to maintain photographic performance over time. Fresh Solution-Newly mixed, unused solution.
KODAK C 41 CONTROL STRIPS PROFESSIONAL
If you are using a KODAK Minilab System 88 or 89, a KODAK PROFESSIONAL RP 30 Laser Printer, a KIS DKS minilab system, a Fuji Frontier, or a Noritsu printer/processor designed for Process CP-48 or CP49E, you will find technical information on using KODAK Chemicals in those systems at under the “Technical Publications” tab. Z-101, Using KODAK SM Chemicals in SM Minilabs. Troubleshooting Processes C-41 and RA-4 Note: If you are using KODAK SM Chemicals, see KODAK Publication No.
KODAK C 41 CONTROL STRIPS MANUAL
Also, this manual contains information on paper processing cycles for KODAK EDGE and ROYAL Papers. This manual contains information on the film processing cycles recommended for KODAK GOLD, ULTRA MAX, ADVANTiX, and KODAK PROFESSIONAL Films. Using KODAK FLEXICOLOR Chemicals and KODAK EKTACOLOR Chemicals in your minilab ensures that your film and paper processes will provide optimum results with the least possible environmental impact. It provides the most commonly needed technical information about film and paper processes for minilabs. USING KODAK CHEMICALS IN MINILABS This publication is written specifically for minilab operators.
